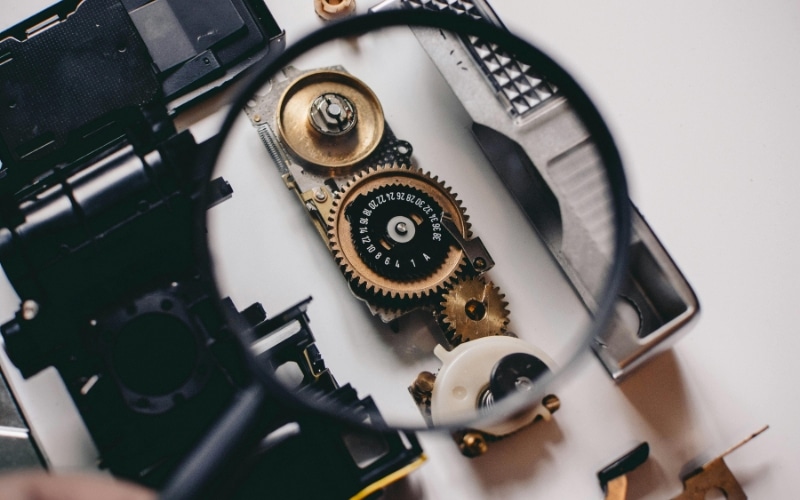
Enhancing Machinery Performance: Strategies for Optimization and Maintenance
In industrial operations, machinery performance directly impacts productivity and profitability. Companies must prioritize optimizing their machinery and implementing effective maintenance practices to stay competitive and efficient.
Here’s a comprehensive guide on how to achieve peak performance through strategic optimization and maintenance, including gear maintenance and rebuilding.
1. Regular Maintenance and Inspections:
Proper maintenance is the cornerstone of machinery performance. Establishing a regular maintenance schedule ensures that equipment operates smoothly and reliably. Routine inspections allow early detection of potential issues, minimizing downtime and costly repairs.
2. Utilizing Advanced Technologies:
Embrace the power of technology to enhance machinery performance. IoT sensors and predictive maintenance software enable real-time monitoring of equipment conditions. Predictive analytics helps in forecasting maintenance needs, allowing proactive interventions to prevent breakdowns.
3. Upgrading to Efficient Components:
Outdated components can hinder performance and efficiency. Upgrade to modern, energy-efficient parts such as motors, bearings, and drives. These upgrades optimize energy consumption and improve overall machinery reliability and longevity.
4. Optimizing Workflows and Processes:
Streamline production workflows to eliminate inefficiencies and maximize machine utilization. Adopt lean manufacturing principles to minimize waste, reduce cycle times, and enhance throughput. This ensures machinery operates at peak efficiency.
5. Employee Training and Skill Development:
Invest in training programs for operators and maintenance personnel. Well-trained staff can effectively operate machinery, diagnose issues promptly, and perform preventive maintenance tasks. Continuous skill development ensures they stay updated with the latest technologies and best practices.
6. Monitoring Performance Metrics:
Track key performance indicators (KPIs) such as equipment uptime, OEE (Overall Equipment Effectiveness), and cycle times. Utilize data analytics to identify performance trends, areas for improvement, and opportunities to optimize machinery operations.
7. Implementing Energy Management Strategies:
Implement energy management strategies to reduce energy costs and environmental impact. Optimize machine settings, utilize variable frequency drives (VFDs), and schedule operations during off-peak hours. Efficient energy management enhances sustainability and reduces operational expenses.
8. Enhancing Gear Maintenance and Rebuilding:
Gears are critical components in machinery. Implement a robust gear maintenance program that includes regular lubrication, inspection, and cleaning. Consider professional gearbox rebuilding services like MayDay when gears show signs of wear or malfunction. Rebuilding involves thorough inspection, replacement of worn components, precise reassembly, and performance testing to restore optimal functionality.
9. Investing in Automation and Robotics:
Integrate automation and robotics to handle repetitive tasks and complex operations with precision and efficiency. Automation improves production consistency, reduces human error, and frees up skilled labor for more strategic roles.
10. Cultivating a Culture of Continuous Improvement:
Foster a culture where employees are encouraged to suggest and implement improvement ideas. Regularly review processes, technologies, and performance metrics to identify opportunities for enhancement. Embrace innovation to stay competitive and responsive to market demands.
By implementing these strategies and emphasizing gear maintenance and rebuilding as integral parts of machinery optimization, companies can achieve significant improvements in performance, reliability, and operational efficiency. This proactive approach enhances productivity and ensures sustained success in today’s competitive industrial landscape.